Automatik Plastics Machinery GmbH
- Industries
- Chimie | Plastique
- Client
- Automatik Plastics Machinery GmbH
Challenge
Functional integration for higher quality and lower costs
Intelligent inverter drive eliminates PLC and HMI
Particularly in these times of globalization, all machine manufacturers are faced with the challenge of raising quality and reliability alike. Automatik Plastics Machinery GmbH in Grossostheim, a manufacturer of pelletizing machines, has found an elegant solution in the form of Yaskawa A1000 inverter drive.
The reliability and quality of a machine can be improved by reducing the number of components. A suitable design principle in this regard is the integration of functions. Individual parts of a machine perform multiple functions, which previously required the installation of numerous different components. An optimized drive system allowed Automatik Plastics Machinery to make significant improvements to its PRIMO range of pelletizing systems. These machines cut an extruded polymer strand into even pellets in the required grain size. These then serve as raw material for plastic injection moulding machines or extrusions lines for polymers, threads, films etc.
Solution
PLC and HMI for control, monitoring and operation
In addition to the main drive and drive controller, the pelletizing systems previously required a PLC for programming, controlling and monitoring the motion sequences as well as a terminal to act as the human-machine interface (HMI). This necessitated careful programming along with elaborate and time-intensive assembly and wiring. The individual components also required the necessary installation space in the pelletizing systems. The sheer number of different components alone carried a high error and failure risk – something which the machine manufacturer was keen to avoid.
Result
Flexible AC drive adaptable to application
Working with the drive experts from Yaskawa, an optimum combination of drive, controller and operating terminal was identified. This now takes the form of the highly flexible A1000 inverter drive. Its firmware allows it to be programmed to suit different applications, thus allowing it to perform the functions of a PLC and a terminal. Thanks to the modular design, the hardware can be enhanced with plug-in cards. This can be used, for example, to integrate a larger number of digital and analog inputs and inputs than that provided by a PLC. The display of the inverter drive serves as the human-machine interface. It can also be flexibly programmed to display different status and diagnostic information as well as dialog functions for operating the pelletizing systems.
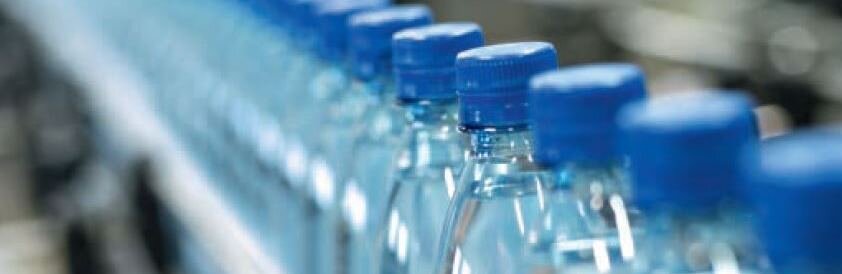
Greater reliability thanks to fewer components
Thanks to the comprehensive integration of functions into the inverter drives, Automatik Plastics Machinery has now identified the ideal means of optimising its pelletising systems. The operation of the machines remains unchanged from previous versions and the machine functions were all integrated as before. Yet the number of components involved was reduced significantly. This raises the reliability of the machines while reducing system downtimes for the operator.
The need for expensive servicing is also minimised, particularly when you consider the large number of machines exported by the company, some as far as Asia and India. This intelligent drive solution established in cooperation with Yaskawa proves that machine manufactures are already more than capable of addressing the growing demand for improved system quality and reliability.