HC10DTP builds RockFarm CO2 storage walls
There is a good idea behind every successful start-up, and at RockFarm there are several of these: the Berlin-based company is building sustainable natural stone walls from CO2-binding lava rock. Or more precisely, it has them built – by a Yaskawa cobot HC10DTP.
When Dr Tobias Brett founded his own company in early 2020, after years in the industry, he already had an ambitious goal: “We wanted to counter the growing global climate problem with a scalable solution.” As a digitalization and automation expert, the industrial engineer also knew that this solution would be high-tech. Today it is a reality.
- Industries
- Protection de l'Environnement
- Construction
- Applications
- Collaboration Homme-Robot
- Client
- RockFarm
- Produit
- HC10DTP - Série HC
Picture: Protected against splash water and dust conforming to protection class IP67 and with a 30 meter long supply cable, the cobot model HC10DTP from Yaskawa is predestined for outdoor use.
Requirements for use and selection of the robot
In addition to the innovative use of accelerated rock weathering, the RockFarm concept has also won acclaim due to a second special feature: the storage walls – some of which are hundreds of metres long – are not constructed manually, but with robot automation.
The developers headed by Tobias Brett have already acquired the necessary know-how in the construction of conventional natural stone walls. In general, they sought to combine a process that was inexpensive, while offering the highest possible quality in finishing, ensuring that the wall remains both marketable and stable for many years.
Special competencies were required in the design of the robot peripherals. This is because the required process times for wall construction can only be achieved with a multifunctional tool that can simultaneously perform three completely different tasks in wall construction. This requirement was solved with an in-house development from the 3D printer.
The search for the actual robot was no less demanding. Because the automated handling of natural materials can cause minor disruptions in the process and necessitate the intervention of a human, a collaborative solution was set up from the start. What was needed was a cobot that could be safely used in the form of a human-machine collaboration (HRC) in direct contact with people.
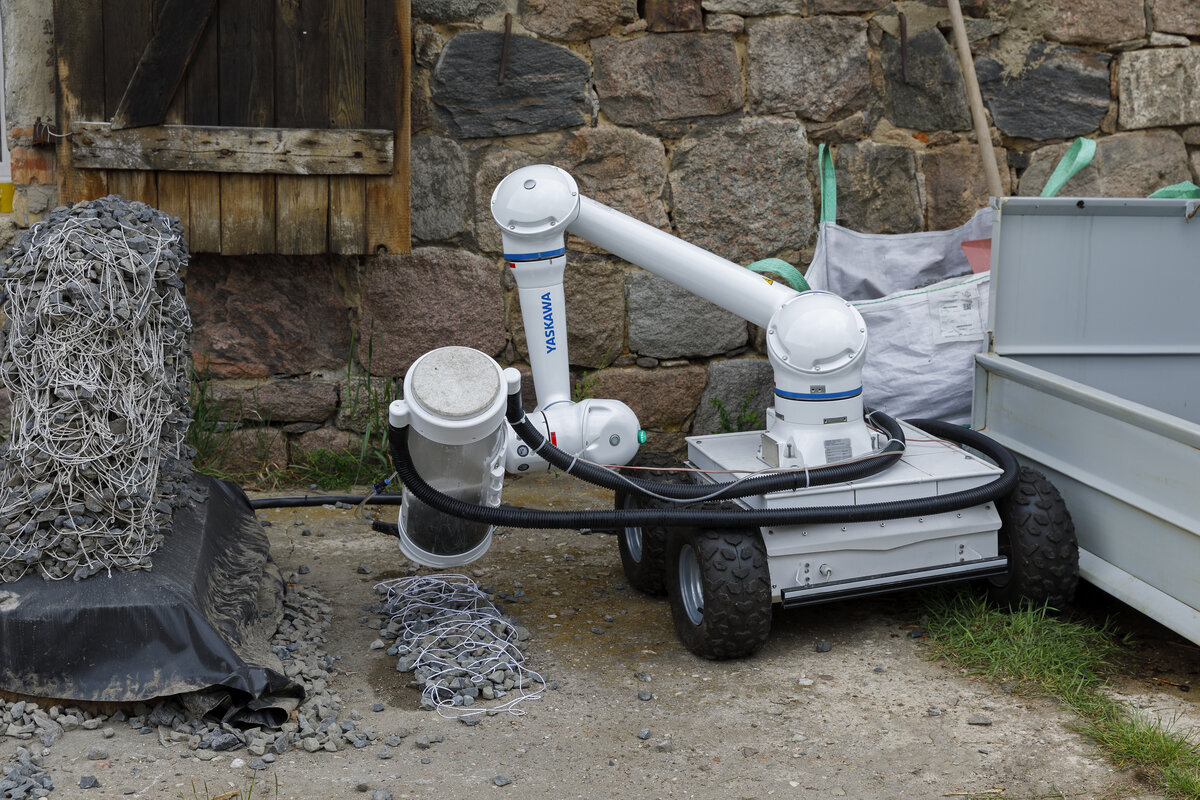
Picture: These walls of volcanic or lava rock bind climate-damaging carbon dioxide (CO2) through accelerated rock weathering, and stores it in the long term.
Decision in favour of the cobot HC10DTP
Although several potentially suitable cobots simultaneously came onto the market, they all had a shortcoming. As Tobias Brett recalls: “Our area of application is outdoors. This means that the robot must still be able to work in a dusty environment or in the rain – which the models we first tested could not.” This only changed with the first cobot from the Yaskawa portfolio: the HC10DTP with a load capacity of 10 kg is designed in protection class IP67 and thus dust-proof and protected against splash water.
Another crucial point spoke for the model: the exceptionally long supply cable that connects the control and manipulator over up to 30 metres. “We were very happy when Yaskawa offered us this variant,” says Brett. This allows the controller to be firmly mounted on a trailer and the entire system to be supplied with mains power. Only the robot moves flexibly – as on a long line – mounted on a mobile chassis. Otherwise, the controller would always have to be moved together with the robot and an additional battery.
Last but not least, the HC10DTP convinced the RockFarm technicians in programming and assembly. Like the other cobot models of the DTP series, it has practical control buttons on the wrist. These make it easier to teach the robot by hand, because not every position on the robot’s hand control panel must be confirmed. The series also features a standardized adapter flange. Peripherals and robots can be easily connected mechanically.
As another advantage, Brett cites the cable and media routing within the robot arm with a range of over 1,300 centimetres. The internal installation of the cables avoids interference contours and additionally ensures robustness in operation.
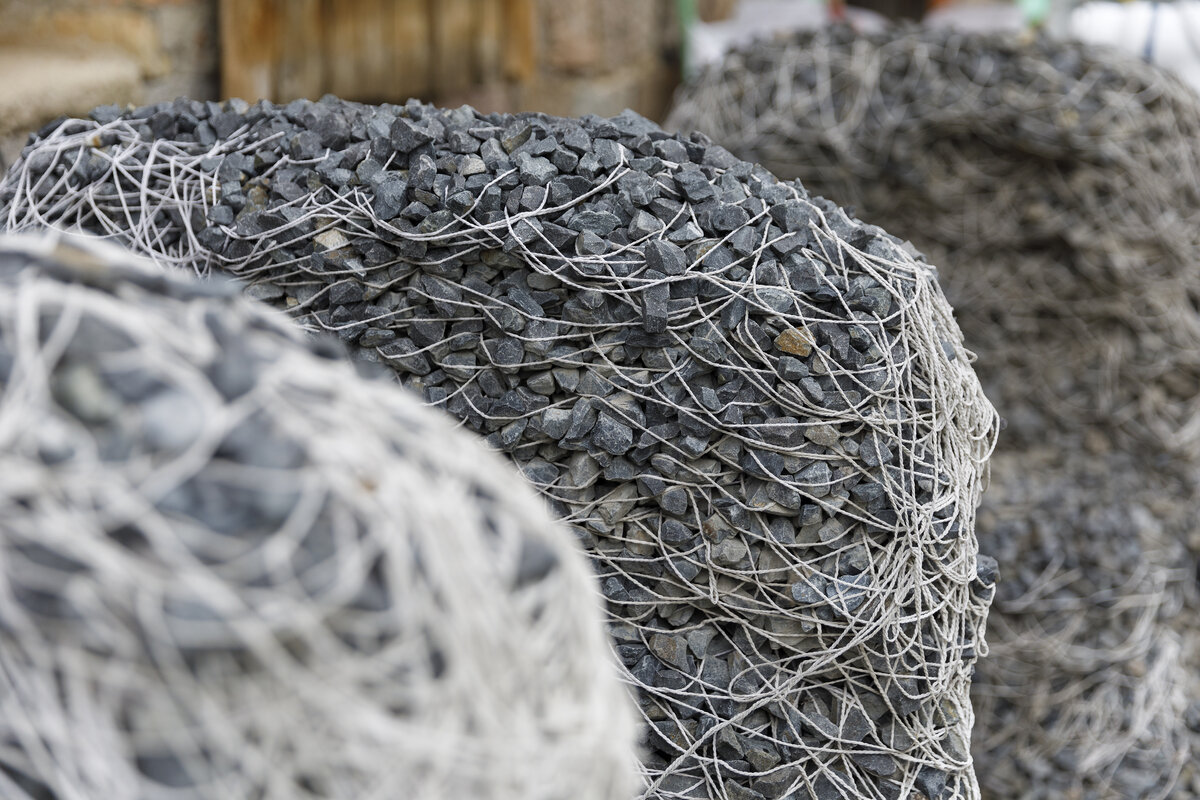
Picture: The required process times for wall construction are achieved with a multi-function tool, an in-house development from the 3D printer.
Conclusion and outlook
Those who pursue ambitious goals – like founder and managing director Tobias Brett with RockFarm – should not be afraid of big comparisons. “Our rock wall solution is inspired by the construction of the Great Wall of China,” the founder and managing director describes the construction process of a ballast fibre composite that has been proven in historical times. Old reports suggest that a Chinese soldier was able to build around three metres per month. A rock wall builder today manually creates about one metre of wall per day. In contrast, over ten metres can be realized by robot automation, depending on the underlying conditions.
The HC10DTP has proven its rock wall building skills several times over, as Brett confirms: “The robot has definitely passed the practical test – even in the rain.” RockFarm now uses the model as standard, and as a positive side effect, the robot attracts attention from potential customers and investors. In addition, the RockFarm concept will also be offered by garden and landscape farmers in a franchise. The use of the robot then ensures the quality of the final product.
The RockFarm team also has an eye on further steps in the future. For example, people are thinking about higher CO2 storage walls, for example for the enclosure of solar systems or as noise barriers on traffic routes. With the HC20DTP, a cobot with 20 kg load capacity and a longer arm with a range of up to 1.9 metres, this would be possible without a problem. Even in other markets, RockFarm has no limits: with Yaskawa, the solution is internationally scalable, because the manufacturer of Motoman robots is positioned worldwide.
Author:
Dr.-Ing. Christopher Schneider (Cobot Business Coordinator),
YASKAWA Europe GmbH – Robotics Division, Allershausen
Contact for readers’ enquiries:
Tel.: +49-8166-90-0
robotics@yaskawa.eu
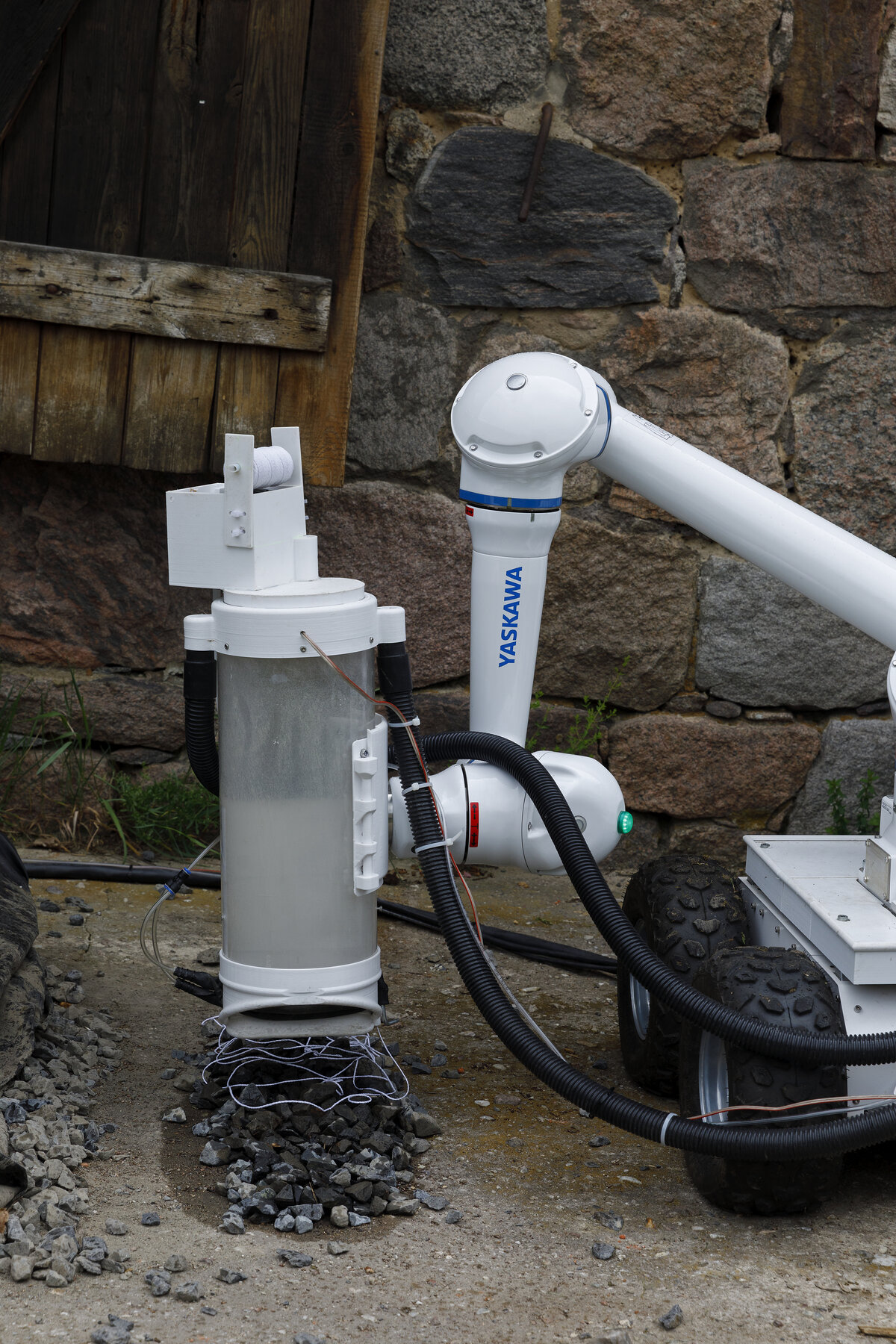
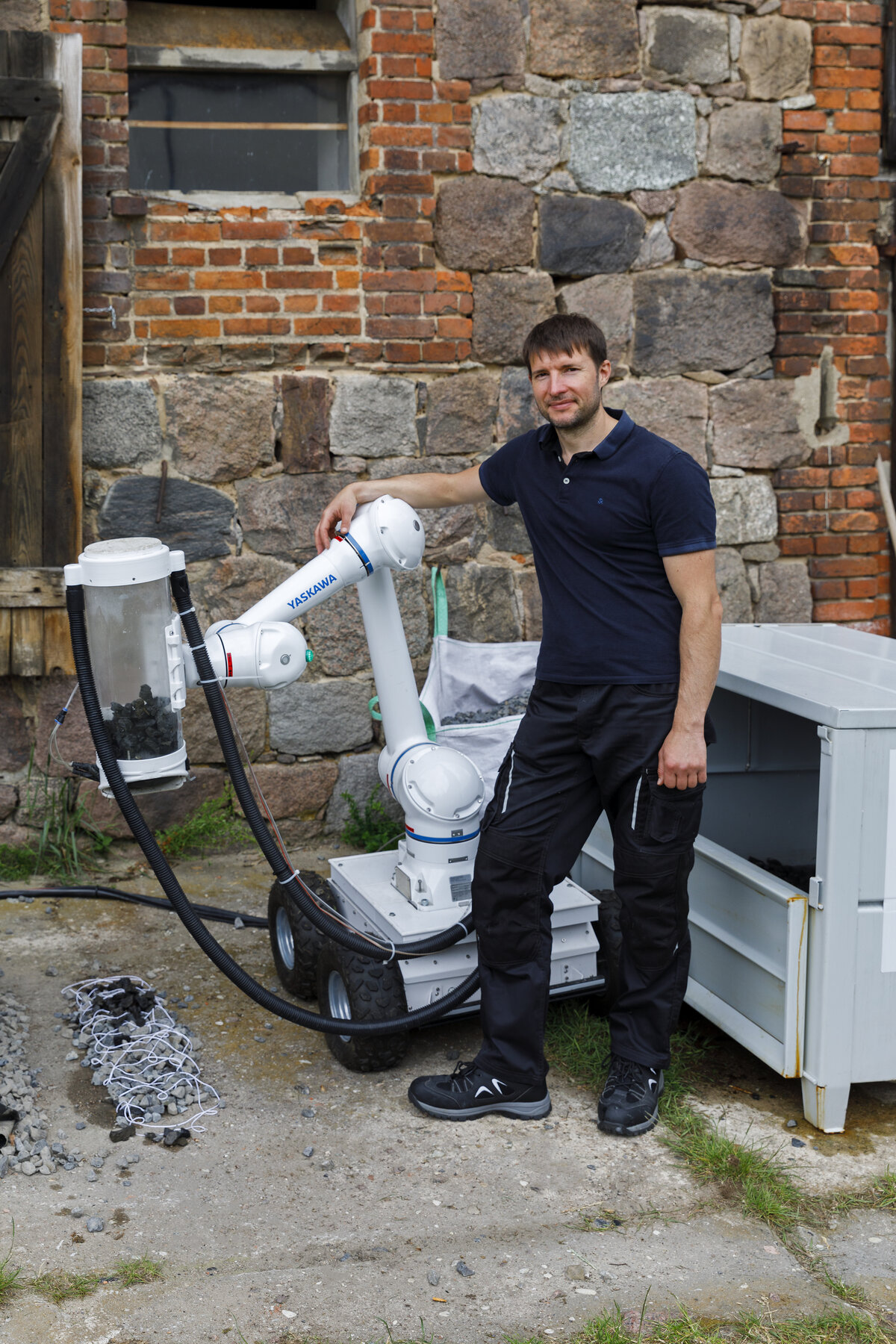