Highly flexible automation for large-scale production of e-bike components
- Applications
- Pick & Place
- Manipulation de pièces
- Client
- Morat Swoboda Motion
- Produit
- DX200 - Contrôleurs de robot
Investment in e-mobility
Morat Swoboda Motion has launched into the age of electromobility with a pioneering automation concept. The manufacturer of drive components for electromobile applications – founded in Nowa Ruda, Poland in 2018 – erected a production facility on a greenfield site.
Morat Swoboda Motion is a joint venture between the Franz Morat Group and automotive supplier Swoboda. For over 100 years, the Franz Morat Group has been among the top drive technology specialists, and manufactures everything from gear wheels to complete drive motors. With a workforce of 4,200 Swoboda develops and produces innovative high-precision components and systems for the automobile future.
With the founding of the joint venture, the two companies have set their future course in the direction of e-mobility. Both the Franz Morat Group and Swoboda have acquired experience in the manufacture of components for electric drive units. “The first joint contract for the supply of gear components for e-bike motors was not only the biggest in the history of the Franz Morat Group, it was also a major challenge for a medium-sized company. That’s why the joint venture was the best solution for all involved,” explains overall project manager Stefan Mayer.
The specific challenge consisted of constructing a manufacturing plant, planning and setting up the production lines and recruiting qualified personnel – all within a tight time frame. Mayer recalls: “There was only a six-month interval between order placement and the ground-breaking ceremony in July 2018. The machines were delivered to Nowa Ruda in November, and the first samples left the plant in March 2019.”
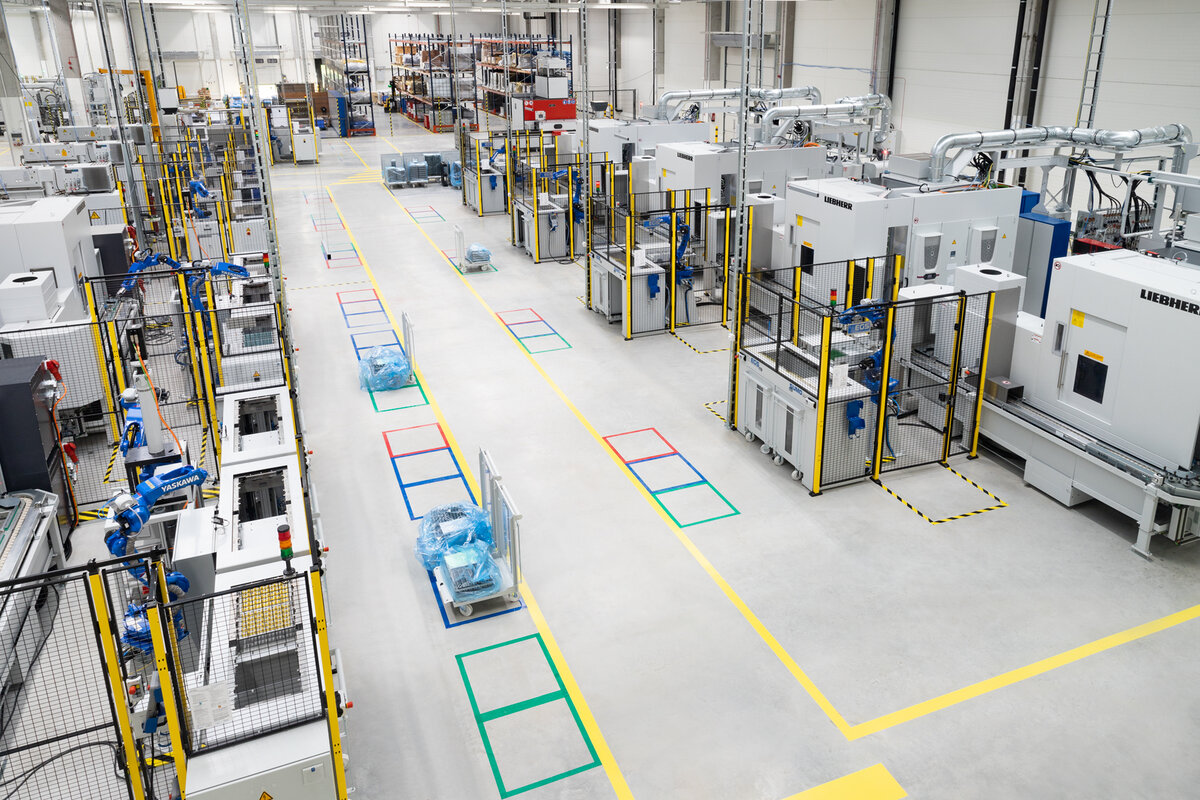
Automation solution in a class of its own
The search for a suitable automation strategy for intelligent and flexible linking of the entire machine park proved to be a major challenge. Moreover, because it called for the highest possible degree of automation with minimum manpower deployment, a suitable fully automatic loading solution had to be found for each machine.
The ideas that were initially discussed consisted of a number of detailed solutions from different manufacturers, but these failed to fully satisfy expectations. However, the presentation of a concatenation concept by Donaueschingen-based EGS Automatisierungstechnik secured the final solution. “Indeed, we were surprised to find that our complex assignment could be resolved using standard EGS modular components,” says Mayer.
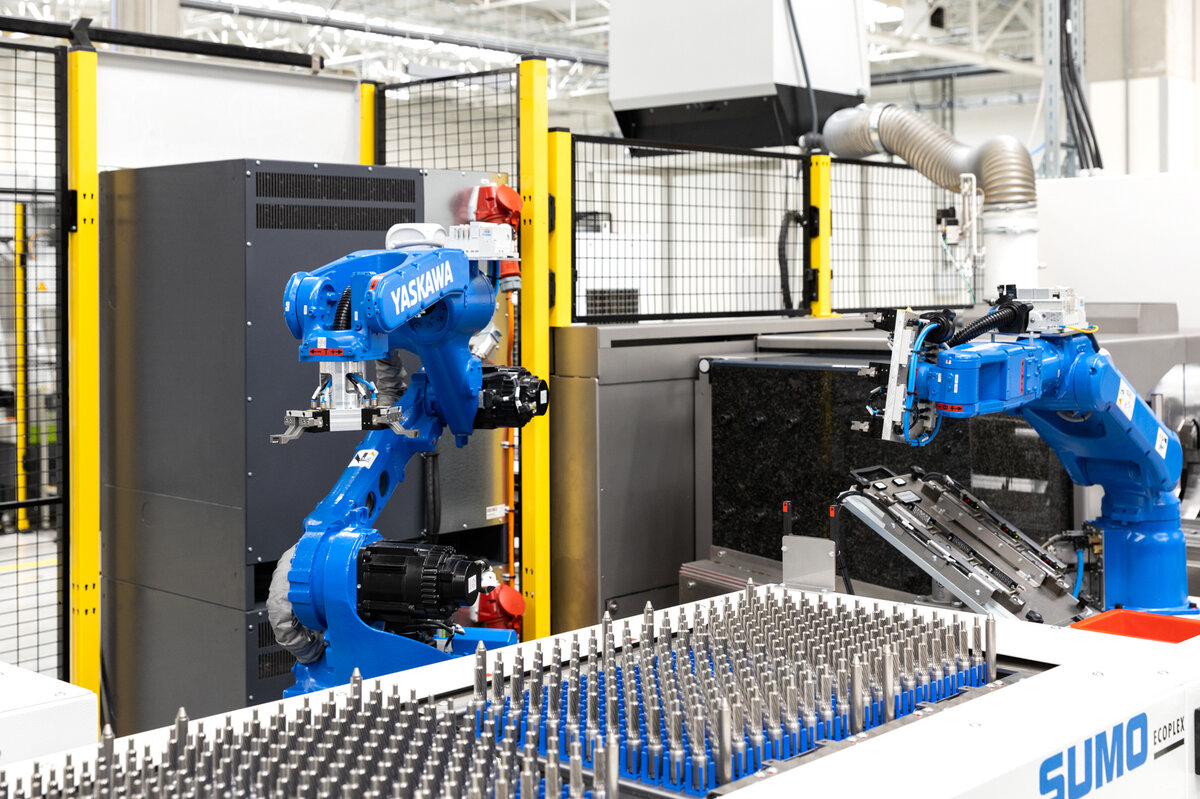
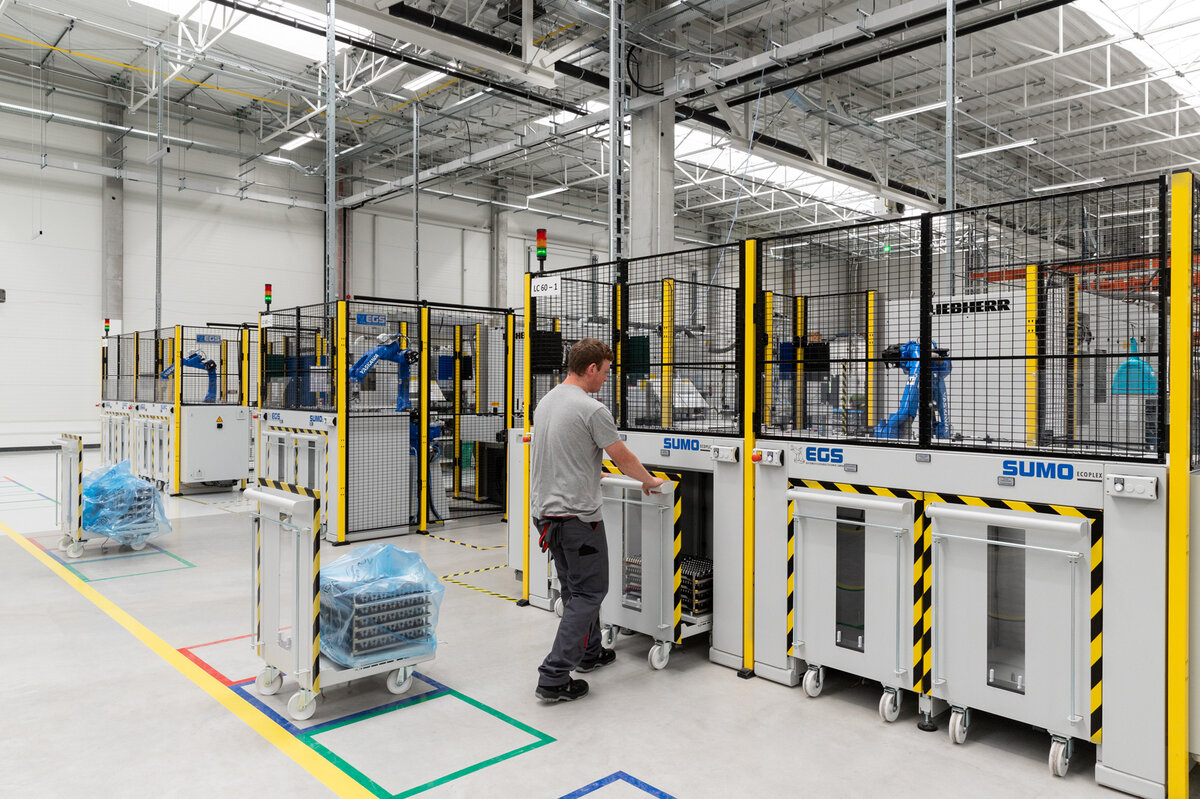
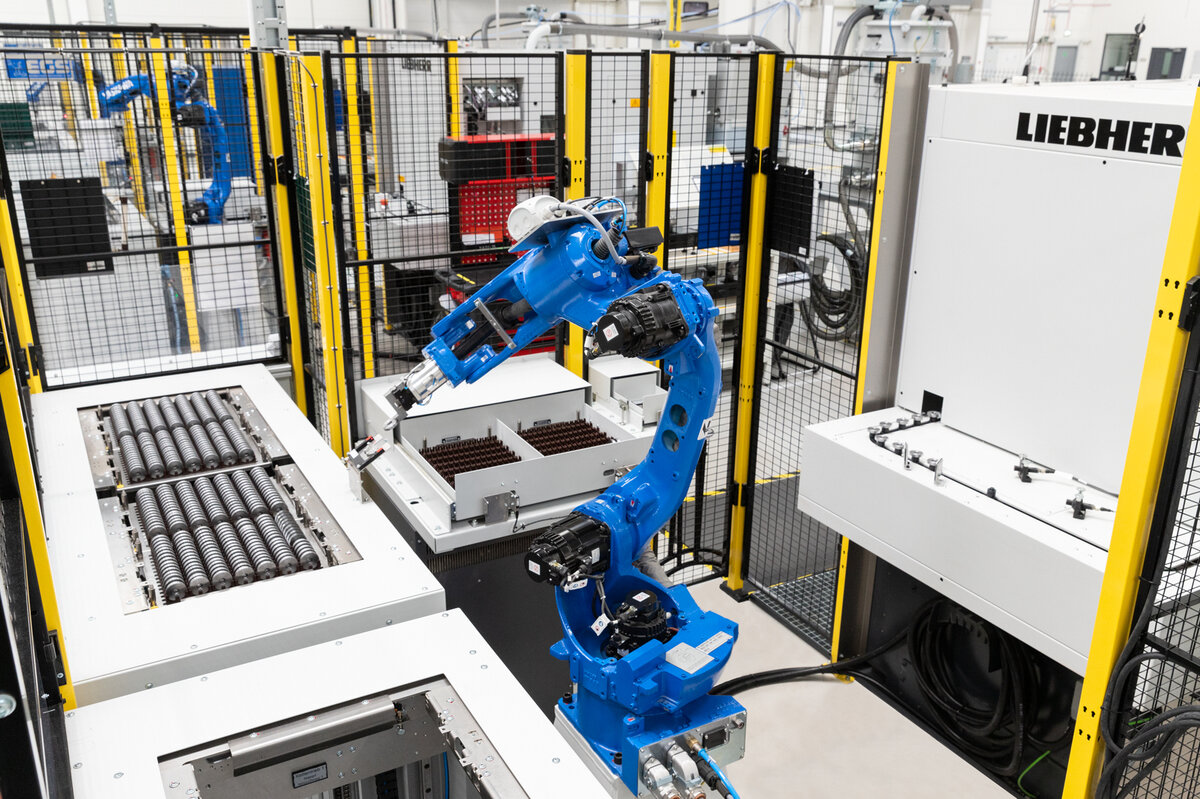
Lean production in the truest sense of the word
The high degree of automation and operator-friendly configuration of the overall system has certainly paid off in the production line with 16 Yaskawa robots and 20 SUMO Ecoplex 2 systems. The machining centre and robot communicate via the Yaskawa DX200 controller.
Quality is a central theme in Nowa Ruda. Although the machine park and robot in combination with an extremely high degree of automation are the epitome of reproducible quality, regular SPC tests are carried out.
Project manager Mayer looks at the future at Nowa Ruda with a mixture of pride and relief: “Production start-up was very successful. All components have fulfilled our expectations. And should there be a sharp increase, as forecast, in the demand for components for e-bikes, we can simply extend our highly flexible modular production,” says Mayer.
Text: Ralf Högel, freelance journalist for Yaskawa Europe; Pictures: Yaskawa