HRC-Palettizing cell by AHM with MOTOMAN HC20 Cobot at Verla-Pharm
- Industries
- Sciences Humaines
- Applications
- Palettisation
- Client
- AHM Sondermaschinenbau GmbH
- Verla-Pharm Arzneimittel GmbH & Co. KG
Robot palletizing without a security fence
Verla-Pharm’s medicines and dietary supplements have been in vogue for decades. But for the industry pioneer, this also means ever increasing throughput and logistics costs as well as the need to ensure optimum utilization of the production space available. In view of this, the tradition-steeped company based in Bavaria is now using a Motoman HC20 palletizing cobot by Yaskawa for the first time.
The blue-and-yellow packaged magnesium produced by Verla-Pharm Arzneimittel GmbH & Co. KG has been on the pharmacy shelves for 60 years. Magnesium Verla® is the market leader among magnesium pharmaceutical products. But the portfolio of the medium-sized pharmaceutical manufacturer has long included a variety of other mineral and vitamin products in varying dosage forms. Selected herbal medicines, natural substances and high-quality food supplements round off the range of products.
Today, some 270 employees manufacture the successful products at modern facilities located in Tutzing on Lake Starnberg. And the company is still growing. So in the course of ongoing development, the previously manual carton palletizing set-up at the end of an existing production line was to be replaced with an automated solution. The main requirements were that it should be as easy to operate as possible and only require a limited amount of installation space.
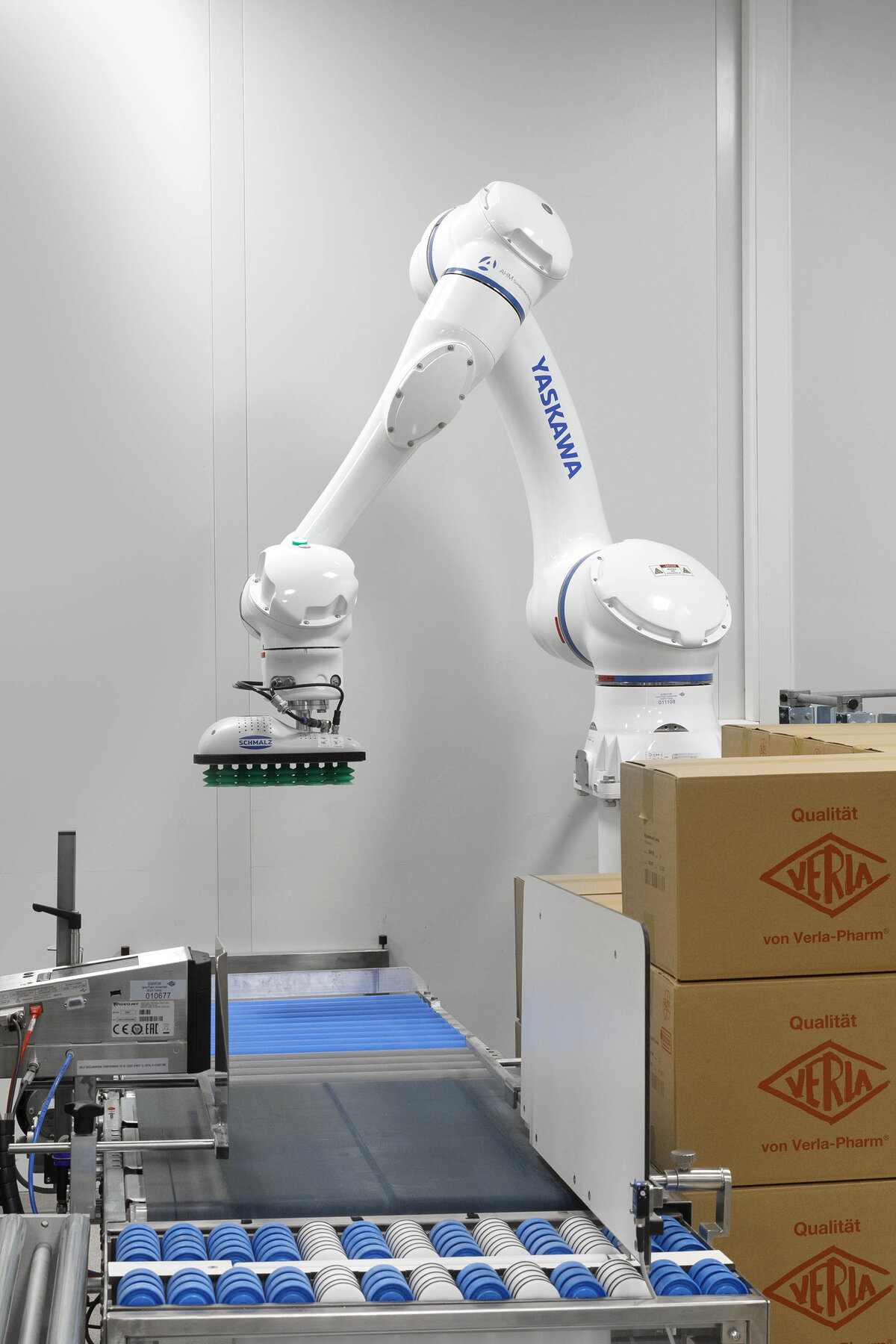
Cobot automation solution by AHM
In the search for a suitable solution, the initial focus was on a classic palletizer with two linear axes. For this reason, those responsible turned to AHM Sondermaschinenbau GmbH in Dasing near Augsburg, which has been developing and producing packaging and palletizing systems of this kind for over 25 years.
“The confined space on site proved to be a major challenge,” recalls Hubert Asam, Managing Director and Project Manager at AHM. As a result, he and his colleagues considered another option: a solution involving a collaborative robot or ‘cobot’ – a robot that allows safe human-robot collaboration (HRC) and therefore direct contact between robot and operator. The advantage: it is perfectly safe for people to approach the manipulator. This means that neither a safety area nor a security fence enclosure is necessary.
Given these benefits, the decision was made to opt for this alternative. As a further advantage, the small system that has been created is very flexible to use: its lightweight construction means that it can easily be moved to other locations within the factory if necessary. And last but not least, according to Managing Director Hubert Asam, it is a “smart, chic solution that fits well into this high-quality production environment.”
The system is very simply constructed: the robot cell consists only of the robot arm (mounted on a base) with matching gripper, controller and operating device. The cartons to be palletized arrive on the existing infeed conveyor and activate the robot by means a light barrier. The robot then transfers the carton onto a pallet, placing it in exactly the right position.
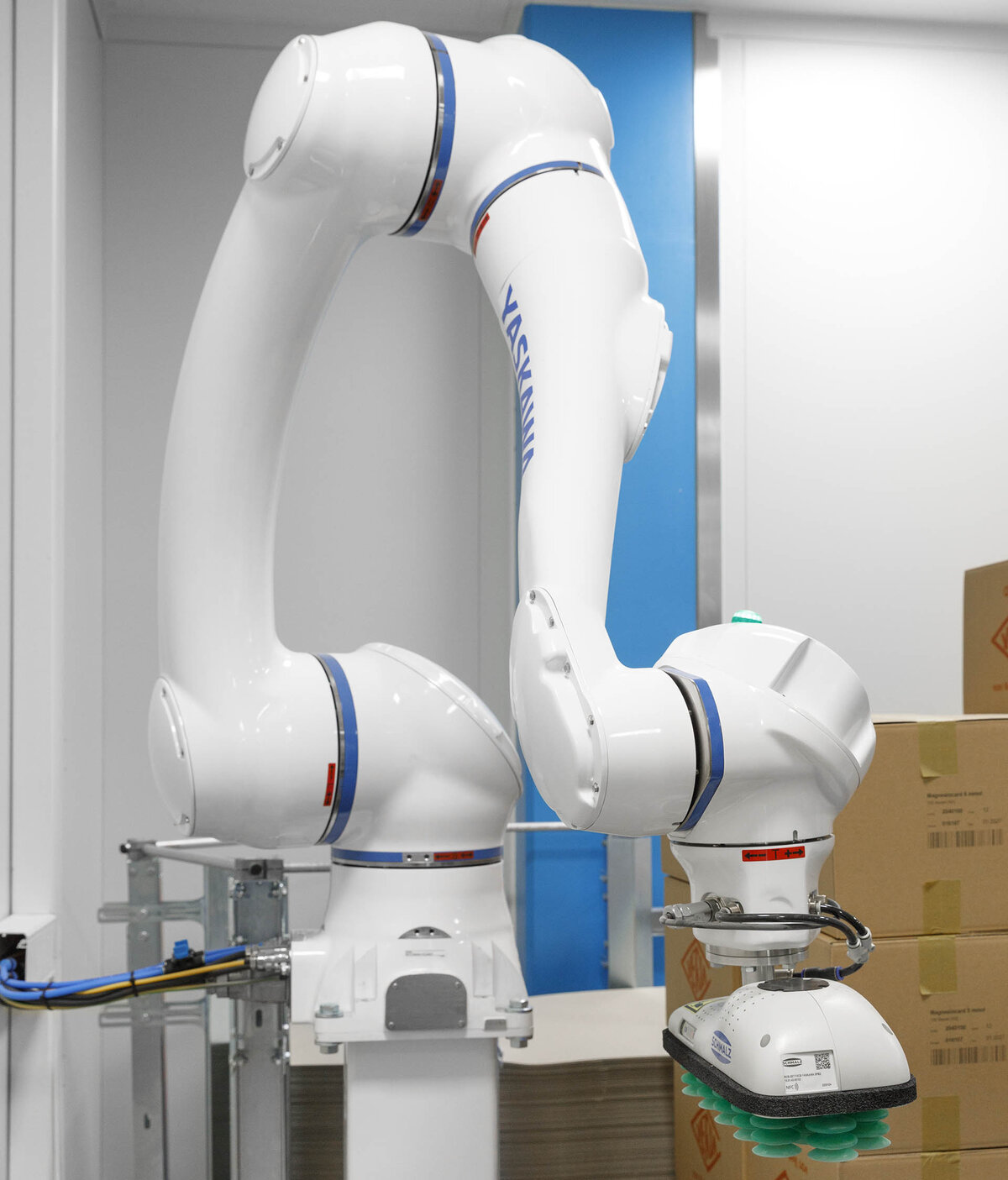
Motoman HC20 palletizing cobot
The cell appears simple at first glance, but its outstanding technical feature is a palletizing cobot from Yaskawa’s Motoman HC (Human Collaborative) robot series. Although it is a full-fledged industrial robot, it is also capable of operating at a safely reduced speed. In the event of any collisions – which are harmless anyway – the manipulator stops immediately, which means it is no problem for people to be directly within its working range.
At Verla-Pharm, the robot runs exclusively in safe, slow mode. The selected model, a Motoman HC20, is highly impressive with its dustproof and waterproof IP67 protection rating, easy-to-clean surfaces and use of food-grade grease (FGG). Above all, the cobot offers an exceptionally high payload of 20 kg combined with a reach of 1,900 mm. “This makes it ideal for this application,” says Hubert Asam. The gripper alone weighs about 3 kg, and together with the cartons for palletizing, this easily adds up to 15 kg. An HRC gripper by Schmalz is used. Like many compatible accessories from the Yaskawa ecosystem, this is perfectly matched with the manipulator. Practical plug & play components of this kind make it easier for system partners like AHM to quickly implement robot installations for a wide range of applications, especially in the area collaborative palletizing.
Like all models in the Motoman HC series, the HC20 offers particularly user-friendly operation: in addition to being operated by means of a clearly structured handheld control unit, the robot arm can also be directly guided and programmed by hand (Direct Teach, DT). This saves time when creating robot programmes. And special machine builder AHM makes things even easier for its customer Verla-Pharm: the processes for a total of three carton shapes are already pre-programmed.
The Motoman cobot ensures the required safety in direct contact with the operator by means of six integrated torque sensors that safely switch off the robot in the event of a collision with persons in its vicinity. This cobot series has been specifically designed for human-robot collaboration (HRC) in compliance with the applicable standards, in particular ISO/TS 15066. Depending on the risk assessment, this type of robot does not require additional protective measures such as a security fence, thereby saving space and costs. The prescribed measurement of possible collision forces during commissioning is normally carried out by Yaskawa using special measuring and testing equipment - “a service we are happy to make use of,” says Hubert Asam of AHM.
Initial practical experience
The new palletizer is not only Verla-Pharm’s first cobot: this is the first time the company has ever used a robot at all. The system has been running trouble-free since installation and has consistently met the company’s high expectations right from the start. The project has been a ground-breaking success for AHM, too: “HRC has potential for the future,” says Managing Director and Project Manager Hubert Asam. “This is what our customers are increasingly asking for. And the solutions in this area are not least a marketing tool for us – especially since Yaskawa’s Motoman HC series robots are so visually impressive, too.”
Authors:
Florian Kohut (Key-Account-Manager Packaging Industry) and Christopher Schneider (Cobot Business Coordinator),
YASKAWA Europe GmbH – Robotics Division, DE-Allershausen
Contact for readers’ enquiries:
Tel. +49-8166-90-0
Fax +49-8166-90-103