MATRIX 18-Pulse Retrofit in water treatment facility
When a Massachusetts based municipal water treatment facility needed to upgrade their aging 350HP 18-pulse drives, they turned to a local Yaskawa drives distributor, who recommended a reliable, compact, and cost effective retrofit with Yaskawa’s U1000 Industrial Matrix Drive.
- Industries
- Protection de l'Environnement
- Produit
- CIMR-UC - Série U1000
Application Challenge
The water treatment facility has four 350 HP pumps. The pumps run 25 MGD on average, but can reach 75 MGD in less than an hour with heavy rain fall. Three of these pumps can satisfy this peak demand. The last pump is used as back-up in case one of the three were to fail. Failure of one pump during peak flow without a back-up could lead to a precarious situation. If the back-up pump and the designated lag pump were to fail, the back-up of the influent main could cause overflowing manholes and flooded streets.
Based on the recommendations of the facility manager, the city made the decision to move forward with updating all of the influent drives. The facility was able to upgrade their aging 350 HP Robicon 18-pulse pump drives, which had become time-consuming and costly to keep in working order.
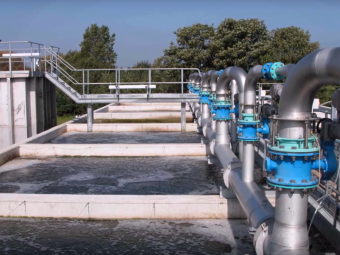
The Solution
The Yaskawa distributor realized that a complete replacement would likely require a different size cabinet. The staff at the facility would also need time to become familiar with it. So they recommended a retrofit option using the Yaskawa U1000 Industrial Matrix drive. After the facility contacted a sister facility which was already using Yaskawa drives, they agreed with the retrofit option.
Since the U1000 drive is a stand-alone, low harmonic drive with regenerative capability, a lot of unnecessary components inside the cabinet were able to be eliminated. The existing circuit breaker from the previous system was also able to be reused.
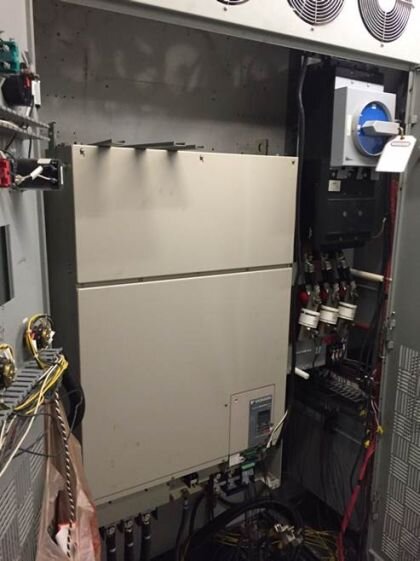
Results
The U1000 solution meets the input harmonic current capabilities of the previous 18-pulse package at rated power and also provides excellent harmonic current levels throughout the load range.
The efficiency improvement was so dramatic that the water treatment facility was able to shut off the additional cabinet fans required to cool the previous system. They realized an immediate increase in efficiency due to reduction of the building’s cooling requirements.
Reusing the existing cabinet saved space, but also meant that virtually nothing had changed for the staff. All the old controls on the door were easily integrated into the U1000.
The Yaskawa solution provided all of these benefits at a cost of approximately half of a new 18-pulse configuration. As a result of this project, the water treatment facility has moved forward with updating several more of their outdated 18-pulse drives with the U1000.
(Source: Yaskawa America, Inc.)