Segbert’s newly-developed CPA-10 cobot palletizer featuring a Yaskawa MOTOMAN HC10
- Industries
- Packaging | Emballage
- Applications
- Palettisation
- Picking | Packing
- Collaboration Homme-Robot
- Client
- Segbert GmbH & Co. KG
- Produit
- HC20DT - Série HC
Full flexibility at top speed
As a specialist for intelligent logistics solutions in the printing and packaging industry, North Rhine-Westphalian machine manufacturer Segbert has had a decisive influence on automation trends in the industry. Now the company has reacted to current market demands for more flexibility in end-of-line packaging with a new cobot palletizer. The centrepiece of the in-house development is an HRC-capable hybrid robot Motoman HC10 from Yaskawa.
All activities of Segbert GmbH & Co. KG, whose headquarters are in Ahaus close to the Dutch border, are focused on the handling of paper and cardboard. Managing Director Klaus Segbert describes the general challenge in the printing and packaging industry as a “rather difficult product”. The company, which was founded in 1968, has taken up the industry-specific challenge by developing intelligent concepts and solutions, in particular for automated stacking and palletizing loose packages and packing units.
New core markets call for compact, flexible systems
Up to now, the Ahaus-based company has mainly specialised in large layer palletizers, of which over 300 are used worldwide, particularly in the printing and graphic design industry. But those in charge at Segbert have long started to focus on new core markets such as the cosmetics and confectionery industries. However, this customer segment has completely different requirements: “Today, in many supermarkets products are commonly sold directly from the pallet, so packaging forms are diverse, including round and open-top packages,” says Klaus Segbert and notes: “With a classical layer palletizer this is not possible.” Instead, compact, flexible and easily movable end-of-line units are required.
With this in mind, the Segbert specialists embarked on a search for potential solutions. It soon became clear that articulated robots would play an important role. However, Klaus Segbert and his colleagues were faced with a general problem: a cobot enables direct human-robot collaboration (HRC), offers a high degree of flexibility and permits a compact design but cannot attain the desired speeds. On the other hand, a classical industrial robot achieves high cycle times, but due to the necessary safety precautions it requires more space and is also less flexible.
Klaus Segbert captures the essence as follows: “We took the added-value approach, i.e. full flexibility at top speed. That was ultimately the deciding factor in terms of our concept, enabling us to set ourselves apart from the competition.” Following an extensive market analysis, the decision was taken in favour of the Yaskawa Motoman HC10 robot model.
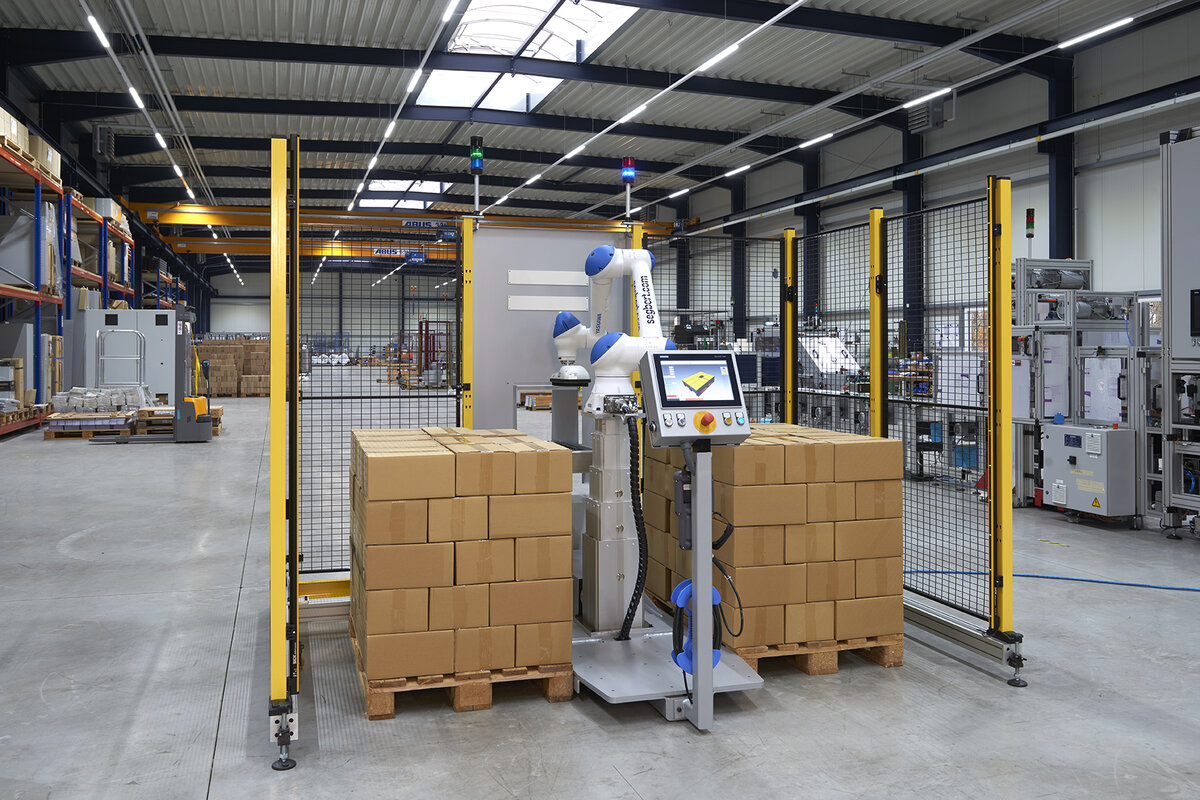
HRC-capable hybrid robot
The Motoman HRC (human collaborative) series comprises HRC-capable hybrid robots. They are full industrial robots that can either operate at a high speed or at a safe, reduced speed whenever a person enters the work area. This area monitoring is implemented by means of external safety sensors, such as laser scanners. In industrial mode, i.e. where humans are not endangered, the robot achieves top speeds of up to 1 m/s.
The hybrid mode, i.e. switchover capability between collaboration and industrial mode, ensures maximum economic efficiency with low space requirements. This is particularly advantageous when integrated into systems where space is limited, precluding the use of safety guards.
The Motoman HC10 provides the required safety in direct contact with the operator by the use of six integrated torque sensors that enable flexible interaction between the robot and its environment. They monitor all external forces that occur, guaranteeing the highest level of safety during direct human-robot collaboration. Within the framework of existing international standards, especially ISO TS 15066, the torque sensors in each joint enable the Motoman HC10 to operate in the fourth collaboration mode “Power and Force Limiting (PFL).
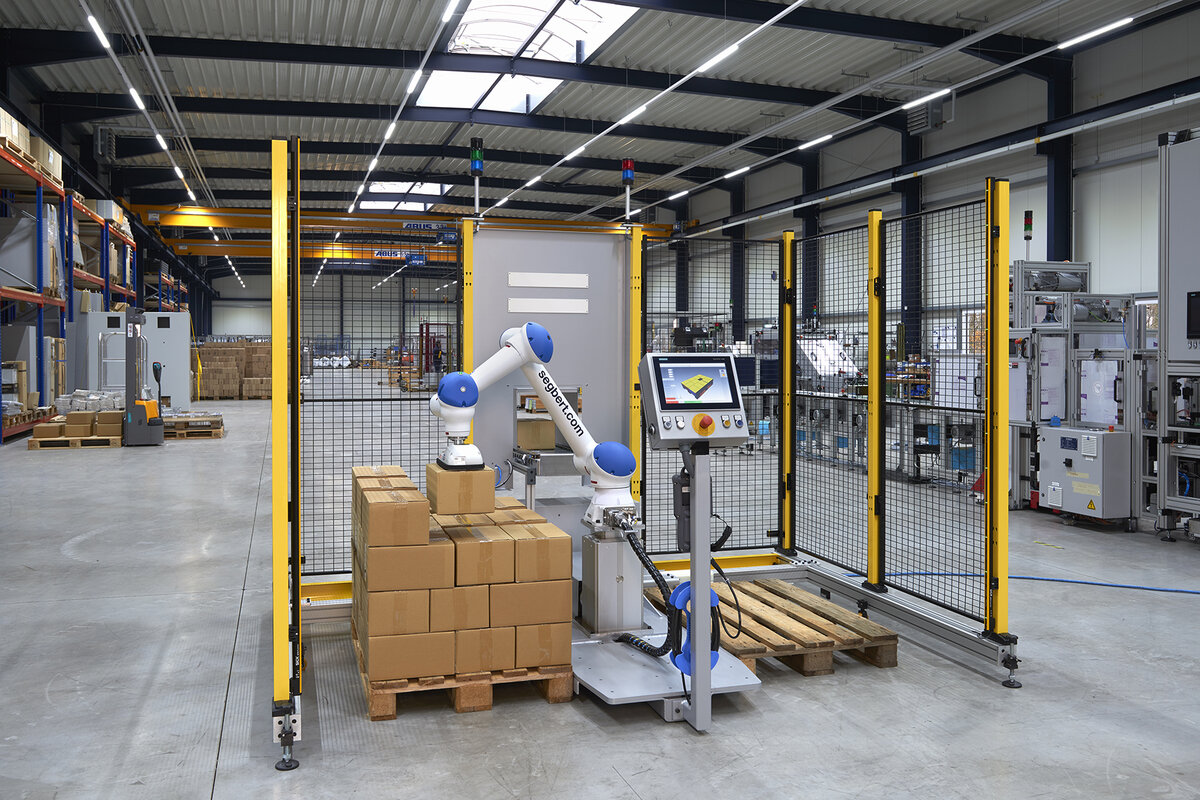
CPA-10 cobot palletizer/depalletizer
The Motoman HC10 was more or less predestined for Segbert’s latest new development, the CPA-10 palletizer/depalletizer. The compact unit enables dynamic palletizing and depalletizing on up to two pallets simultaneously. As a semi-automatic system, it normally operates in the fast industrial mode. When a person approaches, it automatically switches to collaboration mode.
In its current version the CPA-10 is designed for products such as cartons, boxes or other fixed packages that can be gripped with an HRC vacuum suction device. In the version without protective measures or in purely collaborative operation, six products can be palletized or depalletized per minute. Fitted with safety equipment, up to 11 products are possible in industrial mode. As an alternative to laser scanners or pressure mats, Segbert also developed a flexible, integrated safety guard: the entire unit can still easily be moved complete with the safety guard.
The maximum net payload is 9 kg. The robot sits on a moving height-adjustable console that is integrated as a 7th axis into the controller. The manipulator has a maximum reach of 1,200 mm, making it ideal for euro pallets. The unit is flexibly and intuitively operated using the RobAdmin Basic or Pro3D layer program developed by Segbert. For each algorithm the software automatically calculates the ideal layer pattern for the robot. The product management software is additionally integrated.
The robot is operated by a Motoman YRC1000micro high-performance controller that communicates with the programs and system control unit via open interfaces: with a cabinet volume of just 30 litres, it is extremely compact and enables optimum use of space. The hand-held programmer of the YRC1000micro controller – the lightest in its category at only 730g – is ergonomically designed and features clearly laid out operating elements. The touchscreen enables intuitive operation and simple movement and scrolling with the cursor. In addition, the robot arm can be manually guided and programmed (direct teach, DT).
First practical experience and outlook
The first CPA-10 prototypes were delivered in January 2021. Initial customer feedback indicates that the employment of an HRC-capable hybrid robot is spot on: “Present users operate the unit for about half the time in industrial mode and the other half in HRC mode,” Klaus Segbert reports on the first, predominantly positive practical experience.
But the Segbert team does not see this success as a reason to rest on its laurels. Further HRC-capable tools, e.g. a fork gripper for open, non-absorbent cardboard boxes, are at the design stage. And a new version CPA-20 with a larger Motoman HC20 robot and twice the payload is also on the drawing board. For this reason, the successful concept is becoming interesting for markets outside Europe, where larger pallets are usual.
Pictures & Video: Segbert GmbH & Co. KG